金属疲労挙動解明
イントロダクション
金属疲労とは、繰り返し荷重により金属の損傷が蓄積し、最終的に破壊に至る現象です。日航ジャンボ機墜落事故やもんじゅ原子力発電所のナトリウム漏洩事故など、金属疲労に起因する重大事故が相次いでいます。自動車、船舶、航空機など日常生活に密着した多くの構造物には、金属疲労に対する安全設計が求められています。
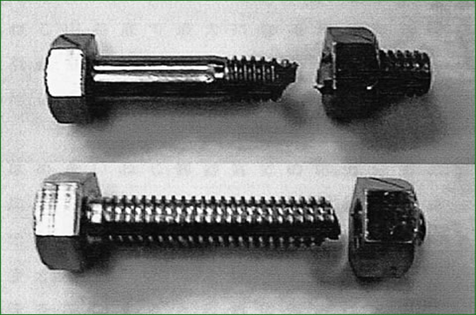
機械構造物は図2に示すように、引張荷重と圧縮荷重の平均応力がゼロにならない非対称のサイクル疲労が起こる環境で使用されることがよくあります。この場合、繰り返し荷重により構造材料は疲労損傷だけでなく、繰り返しクリープ損傷も受けます。これまでの研究結果から、両者の被害には一定の相関関係があると考えられていますが、詳細はまだ明らかになっていません。私たちのグループでは、疲労試験で得られたデータを従来とは異なる解析方法で解析し、疲労損傷とクリープ損傷との相関関係を解明しています。
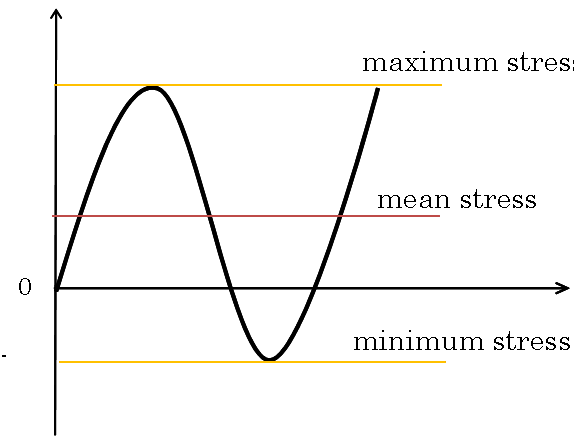
実験
試験材には炭素鋼S25Cを使用しました。試験片を850℃で45分間処理し、その後炉内で冷却してフェライトとパーライトからなる微細構造を形成しました。島津製作所製高温疲労試験機(EHF-EB100kNT-10L型)を用いて、図3に示すような荷重制御疲労試験を実施し、試験片のひずみを連続測定しました。 試験は室温雰囲気で実施し、波形は正弦波、周波数は1Hz、応力比はR=0としました。
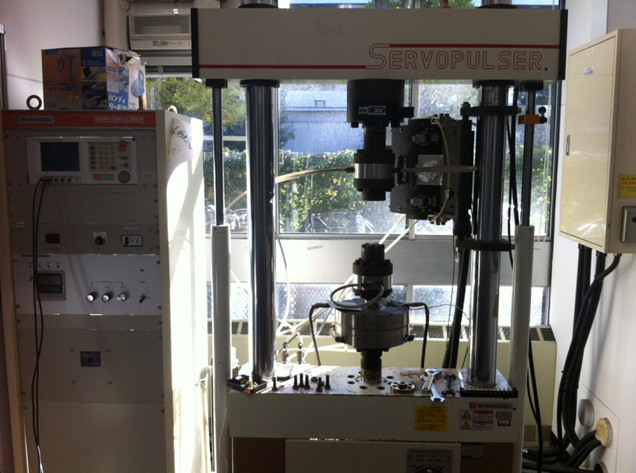
疲労試験から得られた応力とひずみの関係を示すヒステリシスループを図4に示します。これにより、疲労損傷のパラメータである塑性ひずみ振幅 (Δε)とクリープ損傷のパラメータであるクリープ速度 (dεcr/dt) がそれぞれ得られます。
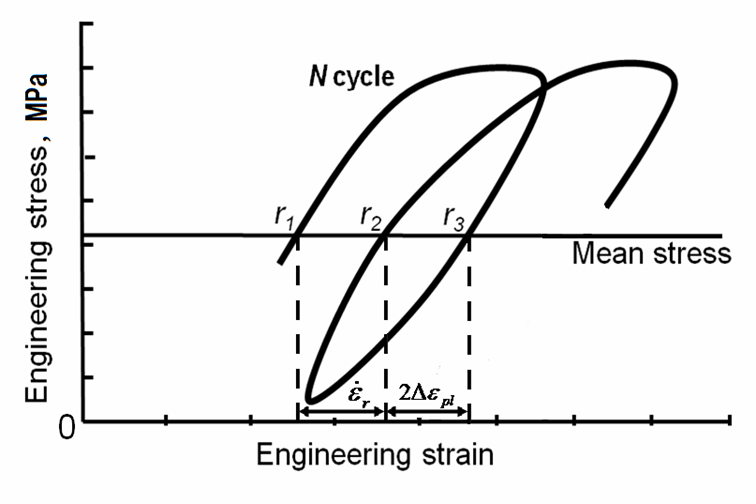
従来、疲労損傷と反復クリープ損傷は同時に発生しますが、両者を別々に解析して比較していました。私たちのグループでは、縦軸にラチェット速度(繰り返しクリープ速度)、横軸に塑性ひずみ振幅の関係を提案することで、従来の解析手法では把握できなかった両者の損傷の関係の解明を試みています。得られた関係曲線は、この解析手法を最初に提案した故堀部進教授の功績にちなんでSH曲線と呼ばれています。
結果
今回の研究で得られたSH曲線を図5に示します。図中の数字はサイクル数を表しており、疲労サイクルの進行に応じて両者の関係が変化することがよくわかります。 従来の解析手法では疲労の進行をき裂の発生,進展および最終破壊の 3 段階に分けることができましたが、この新しいSH曲線では疲労の進行を特徴的な5段階に分けることができます。
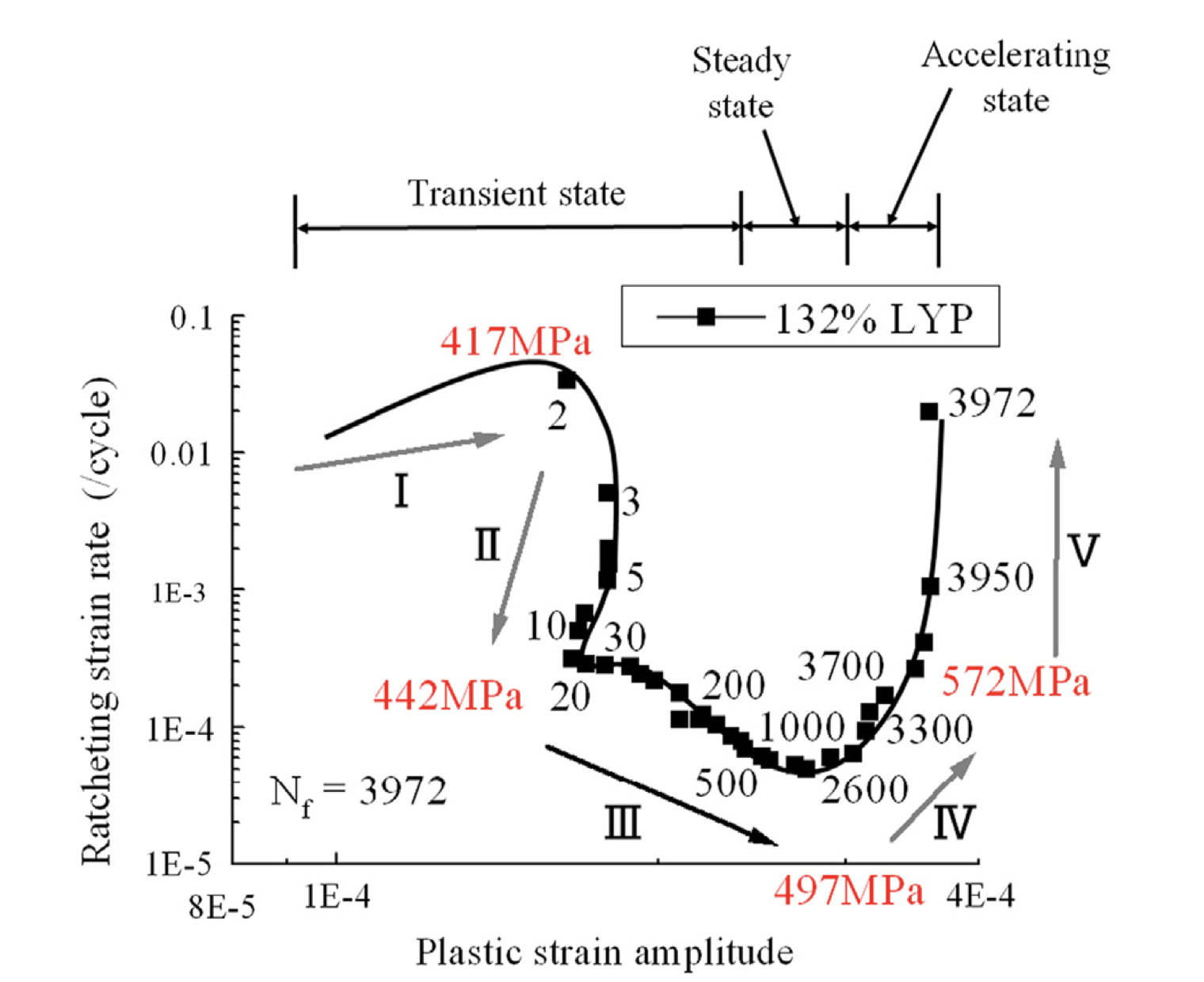
ステージ II および III の微細構造を透過型電子顕微鏡 (TEM) を用いて観察した結果を図 6 に示します。図6(a)より、転位密度が低く、転位セルや転位壁などの複雑な転位構造は観察されないことがわかりました。図6(b)では、粒子全体が転位セルで占められていることが分かりました。
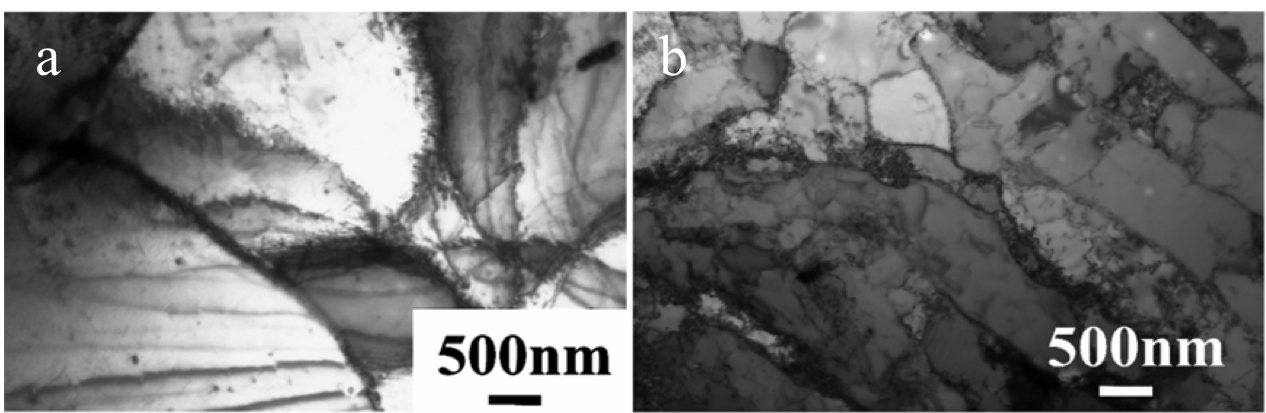
これらの顕微鏡調査の結果と以前の研究の結果を組み合わせることで、各段階は次のように説明できます。
- Stage I: コットレル雰囲気からの転位の除去
- Stage II: リューダース変形の伝播
- Stage III: 多重すべり系による転位セルの形成
- Stage IV: 真応力の増加による転位セルの崩壊
- Stage V: 疲労亀裂の発生と伝播
結論
従来の解析では把握できなかった疲労損傷と反復クリープ損傷との相関関係を解明するために、SH曲線と呼ばれる新しい解析手法を提案しました。現時点では、TEM による顕微鏡観察は応力比 R=0 でしか議論されていないため、片振り荷重 (R≠0) における疲労挙動を理解するにはさらに詳細な検討が必要です。
出版物
- Asato Hara, Rumi Kitazawa, Makoto Yoshida, Susumu Horibe: Material Science & Engineering A 590 (2014) 218-223
- Hiroyuki Shimano, M. Khairi Faiz, Asato Hara, Kyoko Yoshizumi, Makoto Yoshida, Susumu Horibe, Analysis of partially pulsating fatigue process on carbon steel with microstructural observation, Materials Science and Engineering A 651 (2016) 83-88