Copper Alloy Casting Defect Prediction
Introduction
Copper alloy is used for water supply equipment such as water valves due to high corrosion resistance in water and seawater. Casting is one of the method used to produce water valve. This is a technique of pouring molten metal into a mold and solidifying it, in which the metal shrinks when it solidifies as it cools. If this shrinkage is constrained by the mold, stress is generated in brittle metal lump, and defects such as cracks may occur. Particularly, such casting cracks are likely to occur in lead-free copper alloys and bronze developed in recent years, making it difficult to devise an appropriate casting method.
In order to devise such casting method that does not cause casting defects, repetitive time and cost-consuming casting mold prototypes have been proposed. However, in recent years, prediction by casting simulation using FEM has gradually became mainstream.
Therefore, this group aimed at predicting casting defects in copper alloy by casting simulation. In addition, by comparing the result of casting simulation with the result of actual casting, the effectiveness of the simulation are verified. The target alloys are six widely used brass and two of JIS CAC 902 of bismuth-based lead-free bronze.
Experimental
The mechanical properties in the solid-liquid coexistence temperature range that are necessary for the casting simulation were acquired using a semi-solid tensile testing apparatus developed by our laboratory. Fig.1 shows an example of the stress-strain curve obtained in the semi-solidified state.
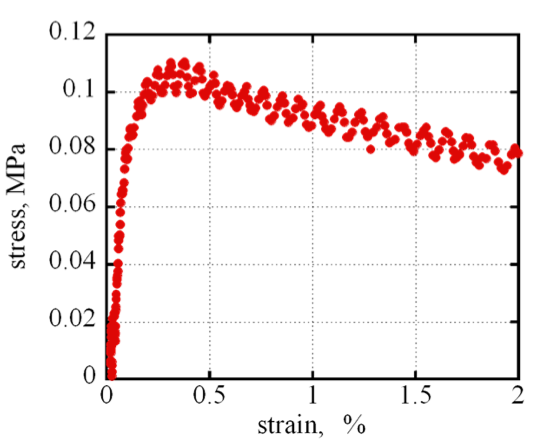
Fig. 2 shows the actual casting shape and the position of defect occurrence. This model is the same model used in simulation and the finding from the experiments are used to validate the simulation results. During casting experiment, the temperature history of castings and molds was also measured.
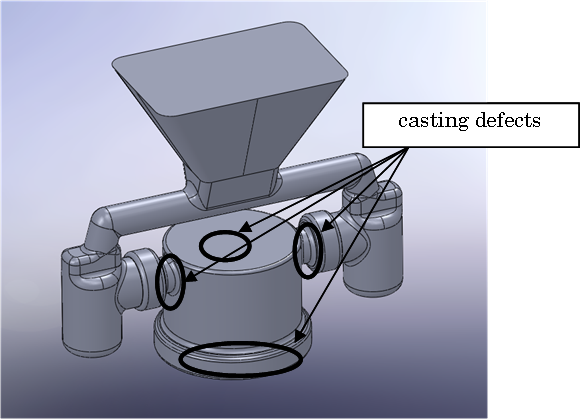
Casting simulation was carried out using elasto-plastic constitutive equation, which was devise from the mechanical properties of the C2800-type brass acquired by the experiment, as explained in 1. Thermal transfer coefficients of analysis were adjusted based on the temperature history during cooling of the C2800-type brass in the die casting test. From the analysis result, the occurrence position of the casting defect was calculated and predicted by calculating the equivalent plastic strain (Hot Tearing Indicator, HTI) generated during solidification. The results are shown in Fig. 3.
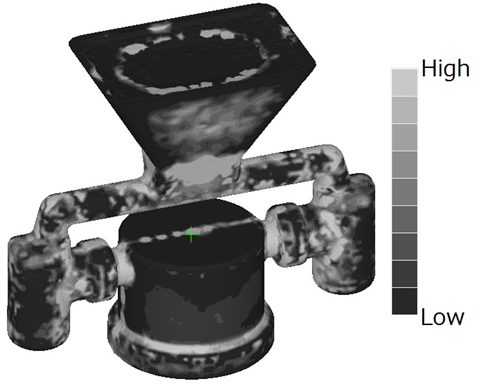
Conclusion
When comparing the casting experiment and simulation results, the positions of the defect occurrence were roughly agreed. To further improve the accuracy of the simulation results, the viscous behavior of castings is ought to be considered.
Publications
- Akira Matsushita, Tomoaki Nakazawa, Toshimitsu Okane, Makoto Yoshida, Crack prediction for a partially solidified lead-free bronze casting using thermal stress analysis, Journal of Materials Processing Technology 249 (2017) 46-56
- Naoki Kasuya, Tomoaki Nakazawa, Akira Matsushita, Toshimitsu Okane, Makoto Yoshida, Mechanical Properties of a Partially Solidified Cu-Zn Alloy, Metall and Mat Trans A (2016) 47: 1661
- Akira Matsushita, Tomoaki Nakazawa, Toshimitsu Okane, Makoto Yoshida, Prediction of hot tearing for a partially solidified bismuth bronze by using finite element method analysis, 72nd World Foundry Congress, WFC 2016. The WFO (The World Foundry Organization Ltd), 333-334