Next-Generation SiC Power Module Development
Introduction
Power electronics module, which is the heart of HEV and EV, is an essential component that processes, converts, and controls the energy in the system. The development of the state-of-the-art wide band gap devices such as silicon carbide (SiC) and gallium nitride (GaN) has enabled power modules for not only achieving higher power density compared to the conventional Si-based devices, but also allowing miniaturization of the power modules, which in return lead to the weight reduction of the vehicles. Fig. 1 illustrates the conventional Si-based and next generation SiC-based power module structure developed by one of power module manufacturing company.
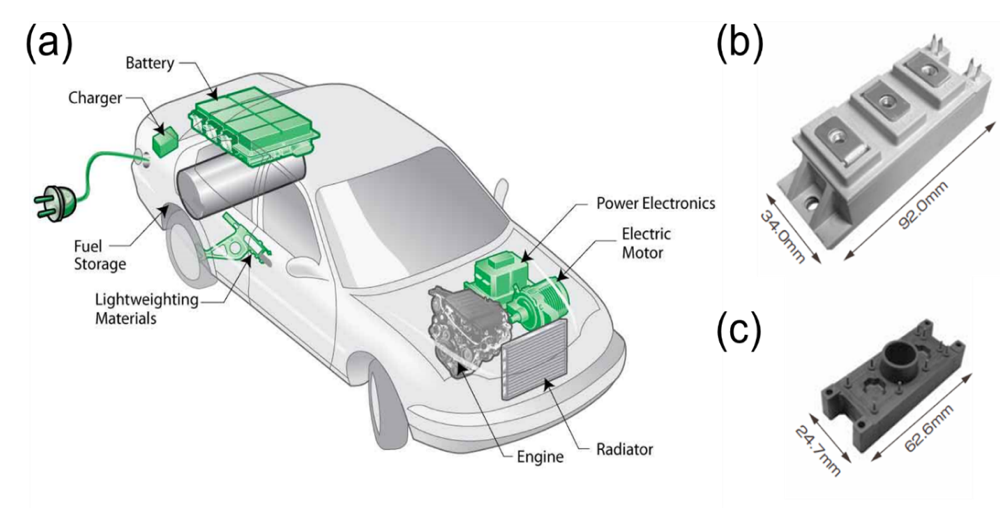
In conventional structure, silicone gel as encapsulation is filled-in the module at the final stage of packaging, usually after bonding the module onto the heat-sink and completing the Al wire bonding (see Fig. 2). However, in the newly developed structure, the module is firstly prepared as a unit module by molding it with epoxy-resin, before being attached to the heat-sink by a thermal interface material (TIM).
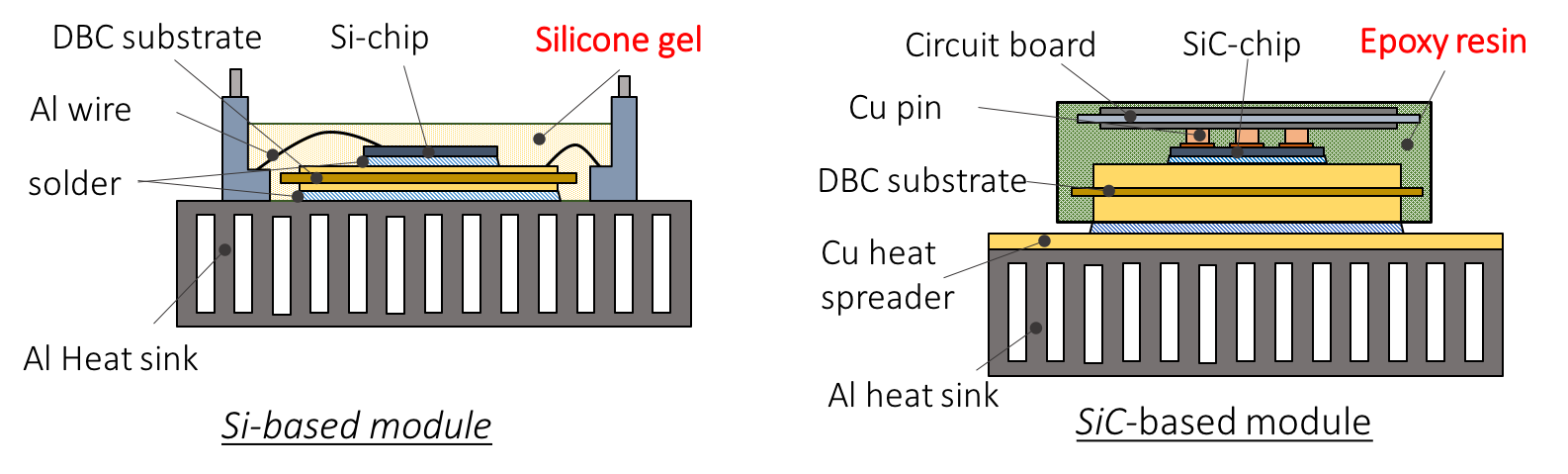
Epoxy-resins that are known to have a low glass transition temperature has inhibited the usage of conventional solder as a TIM. Furthermore, bonding temperature is a crucial aspect in bonding power module as the constituent elements possesses different coefficient of thermal expansion (CTE). Henceforth, to suppress the generation of residual stress during processing, it is essential to reduce the bonding temperature as low as possible. Few other stringent requirements that need to be met in bonding this epoxy-molded module onto the heat-sink is shown in Fig. 3, provided that the top of the heat-sink is attached with a Cu heat-spreader.
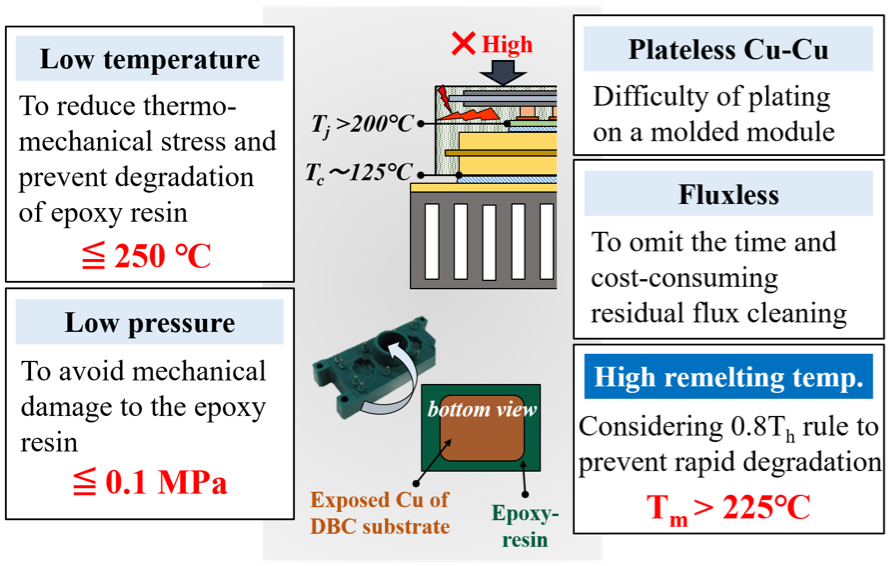
Development of new bonding material
In recent years, Ag or Cu nanoparticle sintering has attracted an immense attention as a die-attach material owing to the possibility of realizing the bonding process at relatively lower temperature than the melting temperature. To top that, the resulted die-attach demonstrates melting temperature equivalent to the bulk material, which is highly favorable for the SiC-based module that generate high heat density during operation. However, one major drawback to utilize Ag/Cu sintering as a TIM is the necessity to apply high sintering pressure during the process to achieve a robust and strong joint. As a solution, in our group, we focus on the transient liquid phase sintering (TLPS) technology to fulfill all the bonding requirements as demonstrated in Fig. 3. The mechanism of TLPS is illustrated in Fig. 4. Our group adapted Ag or Cu nanoparticles as the high-temperature material and mixed with Sn-Bi eutectic powder as the low-temperature material. The influence of processing temperature, time, and other processing conditions on joint strength, remelting temperature and microstructure has been investigated and reported in several publications and conferences as listed below.
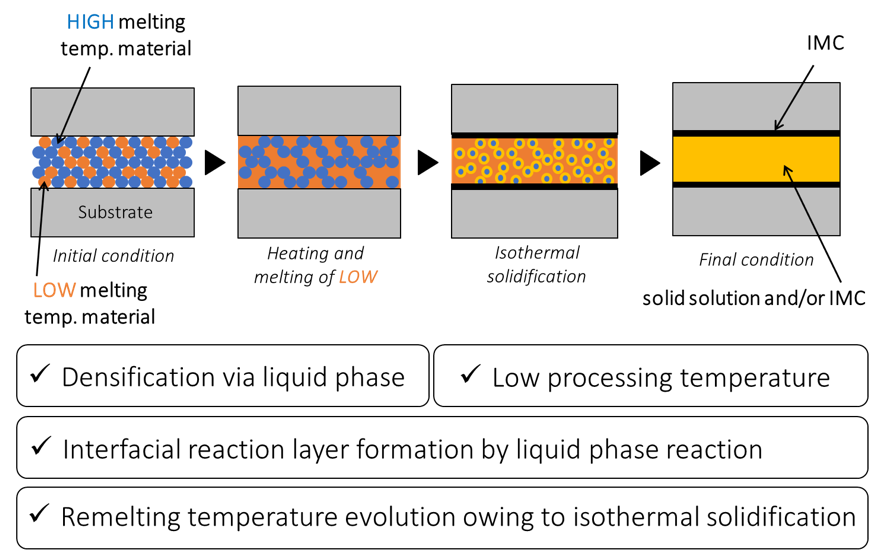
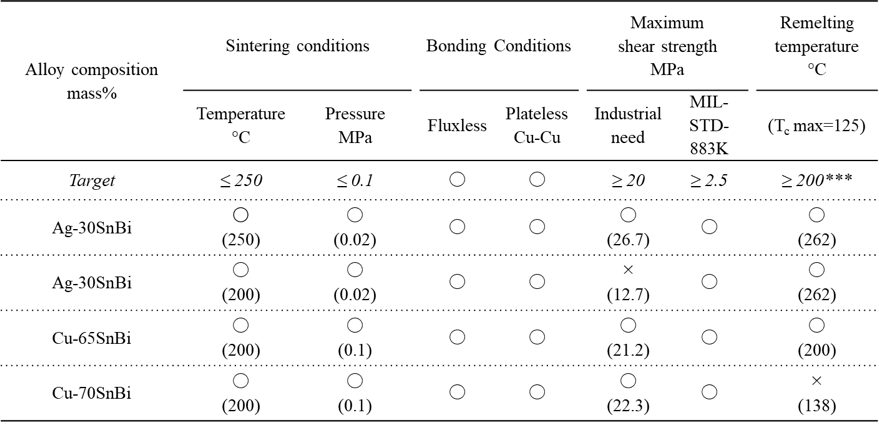
Table 1 shows the results obtained in our group. Cu-65SnBi that was processed at 200 °C has satisfied all the requirements. The usage of formic acid gas that effectively act as a reductant at temperature higher than 150 °C allowing the realization of fluxless process. In comparison with conventional metal sintering where the main mechanism are solid-solid diffusion, in transient liquid phase sintering, the existence of liquid phase of Sn-Bi facilitates the formation of interfacial reaction layer at a shorter time, and in the same time realizes the plateless Cu-Cu bonding, particularly on the Ag-based sintering. On the other hand, it was also found that in Cu-Sn-Bi system, a second liquid phase that is generated at approximately 200 °C has effectively promoted the densification of the sintering microstructure, hence contributed to the strengthening of the joint (Fig. 5). We are working to exploit this newly generated liquid phase to shorten the processing time in the future works by devising an equipment that can allow the bonding to take place when the second liquid phase is generated.
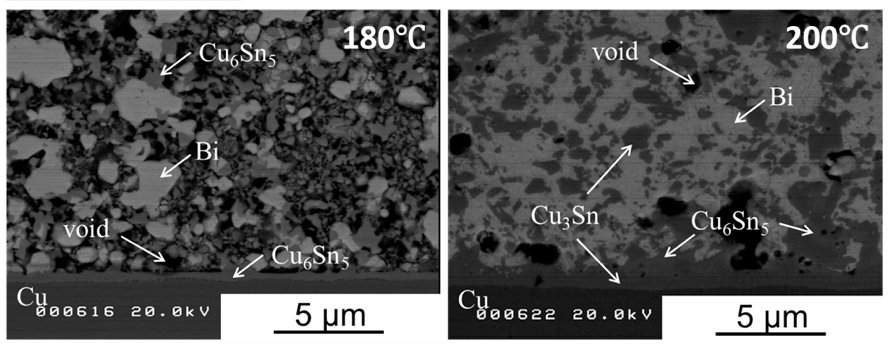
Reliability evaluation of power module
In the development process of power module, reliability evaluation of power module consists of several tests that need to be passed before it can be send off into the market. Power cycle life, and heat cycle life are two type of indexes that are commonly use to evaluate the reliability of power module. The former is the life index of Al wire that are used as wiring on top of the power semiconductor devices where fracture typically generated at the bonding interface. Meanwhile, the latter reflects the reliability of solder that is used as die-attach and substrate-attach, which is acquired by evaluating the heat-dissipation efficiency caused by the crack propagation in the solder. Fig. 6 shows an example of temperature variation in heat cycle test.
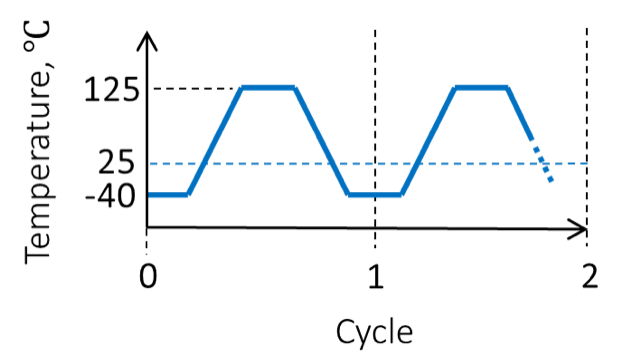
Module is heated in a dry air chamber between -40 °C to 125 °C and temperature is being hold at both low and high temperature regions for several minutes (up to an hour). Solders that are commonly used in power module typically have melting temperature lower than 250 °C, thus even at the room temperature (25 °C), the homologous temperature is approximately 0.5. Meanwhile, recovery of metals is a thermally activated phenomenon, thus, at high temperature region during the heat cycle test, dislocation density in solder is thought to be reduced and solders is expected to “recover”. In addition, two types of recovery are thought to occur, i.e. dynamic and static recovery, where the latter occur during the temperature hold at high temperature region.
Both power cycle and heat cycle tests are time and cost consuming, thus, in order to shorten the production period, numerical solution has become a major substitute to the conventional experimentation. However, an accurate and precise numerical equation to simulate the actual phenomena occurring in the solder during the test is still intensively studied by many researchers. Our group is working on to mimic all plausible phenomena occurring in the solder during the heat cycle test and establish a constitutive equation that can precisely predict the heat cycle life.
Publications, patents, and awards
Publications and Conferences
- M. Khairi Faiz, Kazuma Bansho, Tadatomo Suga, Tomoyuki Miyashita, Makoto Yoshida, Low temperature Cu-Cu bonding by transient liquid phase sintering of mixed Cu nanoparticles and Sn-Bi eutectic powders, Journal of Materials Science: Materials in Electronics 28: 16433-16443, 2017
- Muhammad Khairi Faiz, Takehiro Yamamoto, Makoto Yoshida, Low temperature and low pressure bonding of plateless Cu-Cu substrates by Ag-based transient liquid phase sintering, Journal of Materials Science: Materials in Electronics 28: 9351-9362, 2017
- M. Khairi Faiz, Takehiro Yamamoto, Makoto Yoshida, Sn-Bi added Ag-based transient liquid phase sintering for low temperature bonding, 5th International Workshop on Low Temperature Bonding for 3D Integration (LTB-3D): 34, 2017
- M. Khairi Faiz, Takehiro Yamamoto, Makoto Yoshida, Low temperature and low pressure fluxless Cu-Cu bonding by Ag-based transient liquid phase sintering for high temperature application, IEEE CPMT Symposium Japan, 2017
- Takehiro Yamamoto, M. Khairi Faiz, Tadatomo Suga, Miyashita Tomoyuki, Makoto Yoshida, Low temperature low pressure fluxless and plateless Cu-Cu bonding by Cu nano particle transient liquid phase sintering, IEEE CPMT Symposium Japan, 2017
Patent
Kato Ryoichi, Gohara Hiromichi, Ikeda Yasunari, Mochizuki Eiji, Takahashi Kazuyoshi, Yoshida Makoto, Muhammad Khairi Faiz, Power Electronics Module Manufacturing Method and Power Electronics Module, Patent Application Number 2017-000281
Award
Takehiro Yamamoto, ECR Award, Low temperature, low pressure, fluxless and plateless Cu-Cu bonding by Cu nano particle transient liquid phase sintering, IEEE CPMT Symposium Japan, 2017
References
- Application of Power Electronics in Automotive Applications, (accessed on 31 August 2017)
- Nakano Hayato, Hinata Yuichiro, Horio Masafumi, Ultra-compact, high-reliability all-SiC module, Fuji Electric Review Vol. 59 No. 4 (2013) 221-225