New Aluminium Alloy Development
Introduction
Among aluminum alloys for die casting, Al-Si-Mg die casting alloys (JIS ADC 3 etc.) are known to be more ductile than Al-Si-Cu based die cast alloys (JIS ADC 12 etc.). In addition, with additional T6 heat treatment, appropriate strength can be obtained, hence, the former are commonly used for automobiles chassis parts and motorcycles body parts.
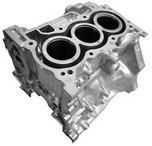
Die casting materials have been considered to be difficult to be subjected to heat treatment. In recent years, various die casting methods such as a vacuum die casting method and pore free (PF) die casting method have been studied and developed. This has enabled heat treatment and welding of a die cast product. Although T6 treatment is often used for heat treatment, occurrence of thermal strain due to water quenching during T6 treatment is a problem. T5 treatment omits the solution heat treatment and water quenching steps that are compulsory in T6 treatment. Accordingly, it is expected to reduce the thermal strain caused by water quenching and also cut the cost by the simplified process.
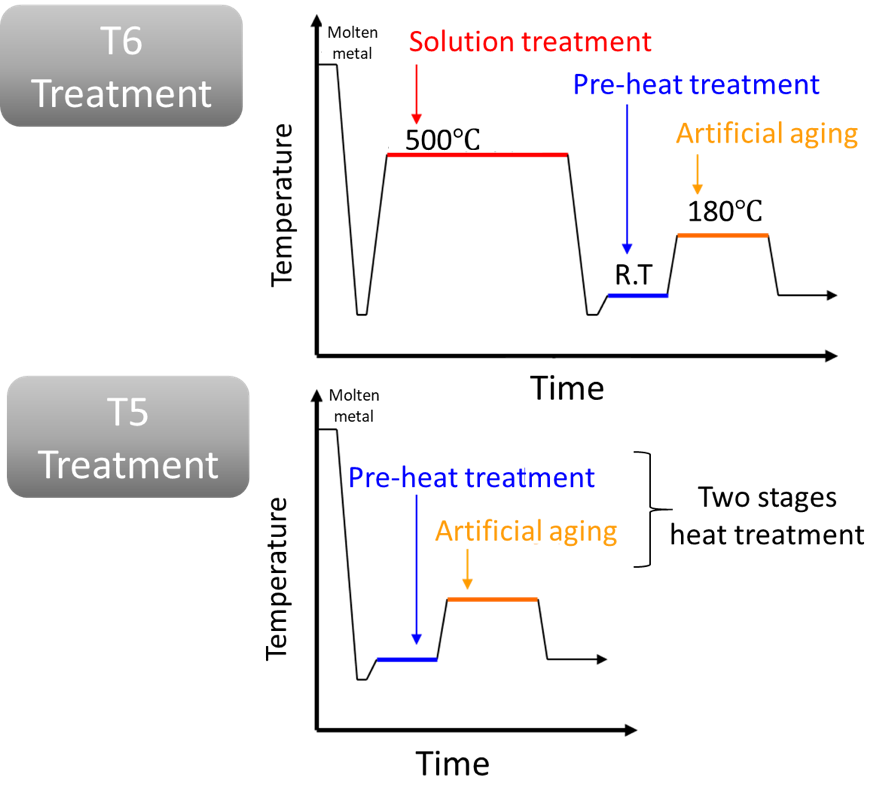
In addition, in T5 and T6 treatment, preliminary aging at room temperature before the test piece is subjected to the actual artificial aging is known to influence the mechanical properties after the artificial aging. However, there are few reports on the influence of preliminary aging in T5 heat treatment of Al-Si-Mg based cast alloys.
Our group investigate the effect of preliminary aging temperature and time on T5 and T6 treatment of Al-9%Si-0.3%Mg die cast alloy and elucidate the two-step aging behavior and the strength-contributing factor in T5 treatment.
Experimental
Materials under test
Al-9.0%Si-0.3%Mg alloy with melting temperature of 998±8 K as shown in Table 1 was die casted into the mold that was kept at 443±10 K. Oxygen-blowing was conducted during the die cast process, and within 1-2 seconds after demolding, the die-casted product was water-cooled at temperature below than 303 K. After water-cooling, die-casted product was fettled and machined into the shape and dimension as shown in Fig. 3. To minimize the effect of natural aging, it was stored with dry ice.
Si | Mg | Fe | Mn | Cu | Ti | Zn | Sr | Al | |
---|---|---|---|---|---|---|---|---|---|
Al-9.0%Si-0.3%Mg | 9.2 | 0.32 | 0.07 | 0.39 | <0.01 | <0.01 | <0.01 | 0.014 | Bal. |
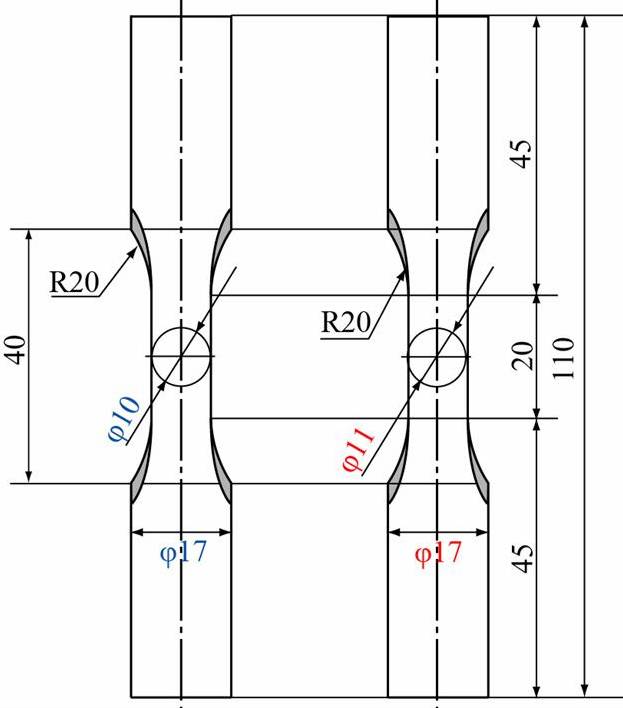
Heat treatment
To investigate the influence of preliminary aging condition in the T5 treatment, test piece was aged from 0 to 345.6 ks at three different temperatures, i.e. 273, 303, and 343 K after water cooling. Next, artificial aging was conducted at 453 K for 10.8 ks in a forced-circulation incubator. It should be noted that the time to raise the temperature to 453 K was 1.2 ks. On contrary, in T6 treatment, at first, the test piece was subjected to solution heat treatment at 783 K for 14.4 ks, and subsequently quenched in water with temperature of 303 K. Then, the same process as T5 treatment explained above was performed. It should be noted that the time to raise the temperature to 473 K during the solution heat treatment was 1.8 ks. A summary of the experiment flow is shown in Fig. 4.
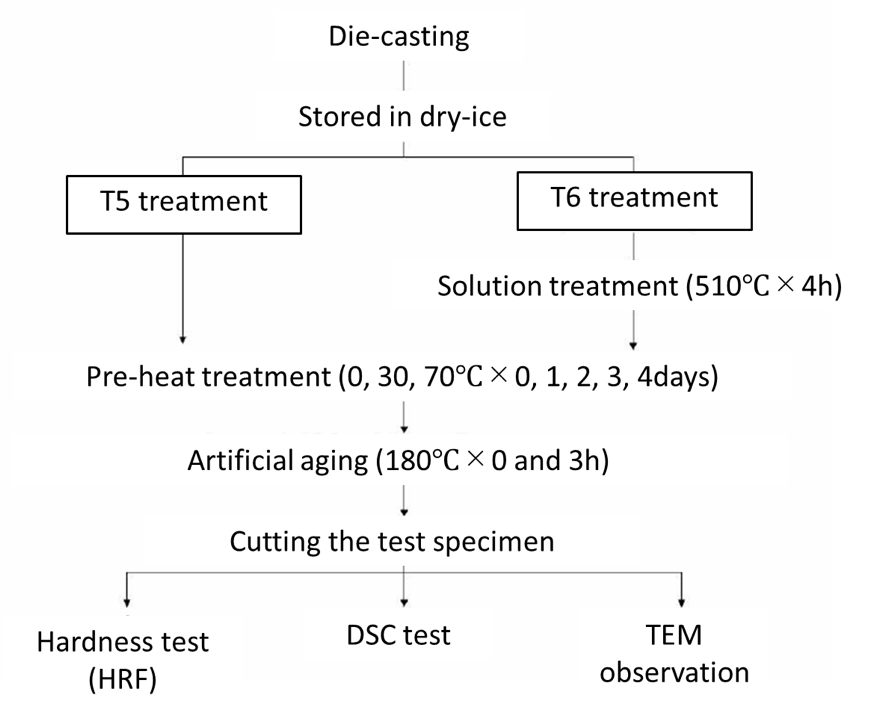
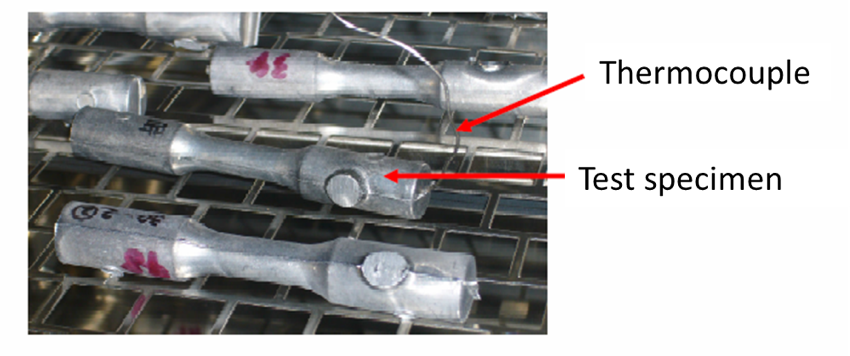
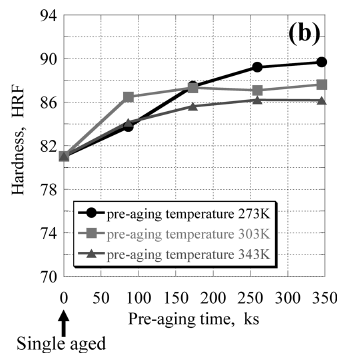
Conclusion
In this study, we conducted a T5 treatment on Al-9.0%Si-0.3%Mg die cast alloy and investigated the heat treatment behavior. The results were as follows. Compared to the case where preliminary aging was not applied, the hardness after artificial aging in T5 treatment was higher when 273 to 343 K preliminary aging was applied, showing a positive effect in two-stage aging. This two-step aging behavior is thought to be the aging behavior peculiar to the T5 treatment.
Publications
- Inoue T., Goto M., Yamaguchi A., Otake T., Kuroda A., Yoshida M., Effect of pre-aging conditions on T5 heat treatment behavior of Al-9%Si-0.3%Mg die-casting alloy, Journal of Japan Institute of Light Metals. 2011, vol. 61, no. 10, p. 507-512.