残留応力予測
当研究室では、自動車部品の製造において従来から行われている鋳造・熱処理工程で鋳造部品に発生する残留応力に着目しています。鋳造と熱処理の両工程で鋳造部品に発生する残留応力や変形を予測する目的で、CAEを用いた熱応力解析を行っています。私たちのグループは以下の6つのサブグループに分かれています。
イントロダクション
現在、FEMを用いた熱応力解析により、鋳造工程で鋳造製品に発生する残留応力を予測することが一般的に行われています。構成方程式とは、金属の機械的挙動を数学的にモデル化したものであり、コンピュータシミュレーションを行う上で必要不可欠なものです。従来の構成方程式では、図1に示すように高温で発生する非弾性ひずみが室温での降伏応力の上昇にも寄与しています。この問題を考慮せずに計算機シミュレーションを行うと、室温での降伏応力が上昇し、計算上の残留応力が大きくなってしまいます。したがって、高温で発生する非弾性ひずみが室温での降伏応力上昇にどのように寄与しているかを考慮できれば、残留応力予測精度の向上が期待できます。当グループでは、ダイカスト用アルミニウム合金(JIS AD 12.1)の室温での降伏応力上昇に及ぼす高温で発生する非弾性ひずみの影響について検討しましたので、以下にその結果を紹介します。
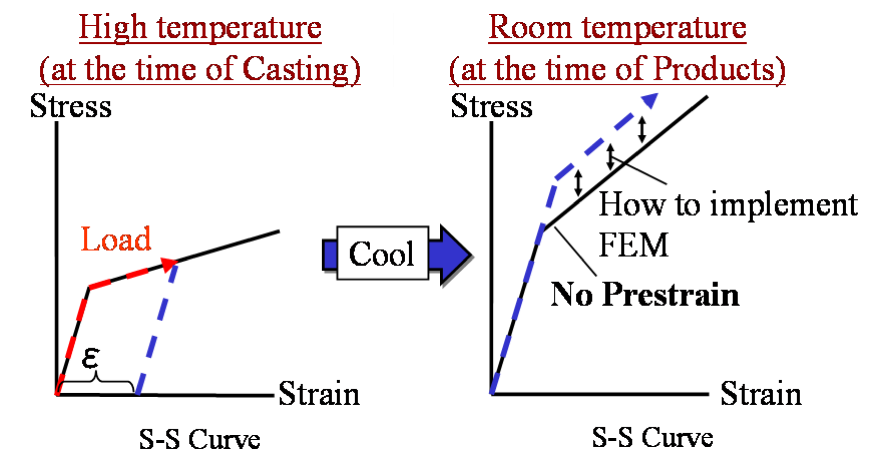
実験
図2に実験の流れを示します。図3に示すように、高温(200, 250, 300, 350, 400, 440 °C)で試験片に予ひずみを加え、時効による硬化を防ぐため試験片はその後凍結されました。次に、室温で引張試験を行い各条件で0.2%耐力を求めました。得られた0.2%耐力を、予ひずみを加えない場合と比較しました。
図4は、各温度における予ひずみが室温での0.2%降伏強さに及ぼす影響を示したものです。図4に示すように、400℃以上で発生する非弾性ひずみは硬化に寄与せず、400℃未満で発生する非弾性ひずみは硬化に寄与します。また、300~400℃で発生する非弾性ひずみはひずみが大きくなっても硬化量は増加しない一方、300℃未満で発生する非弾性ひずみはひずみが増加するにつれて硬化量が増加します。
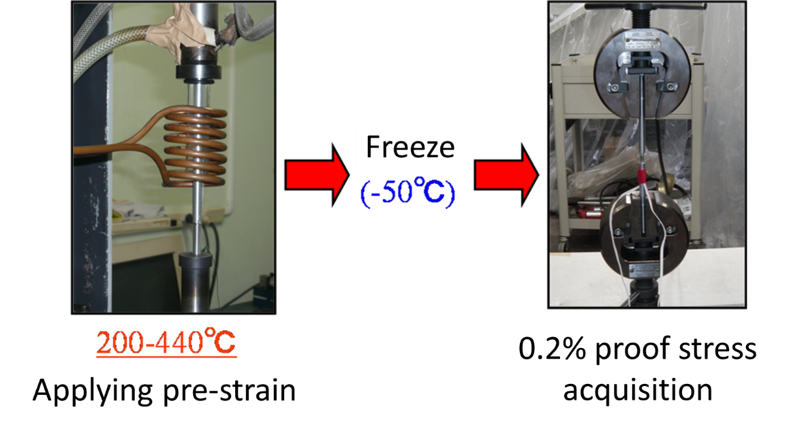
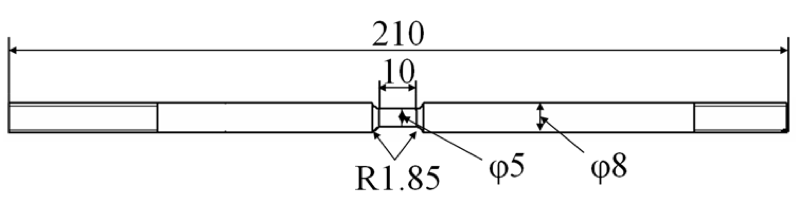
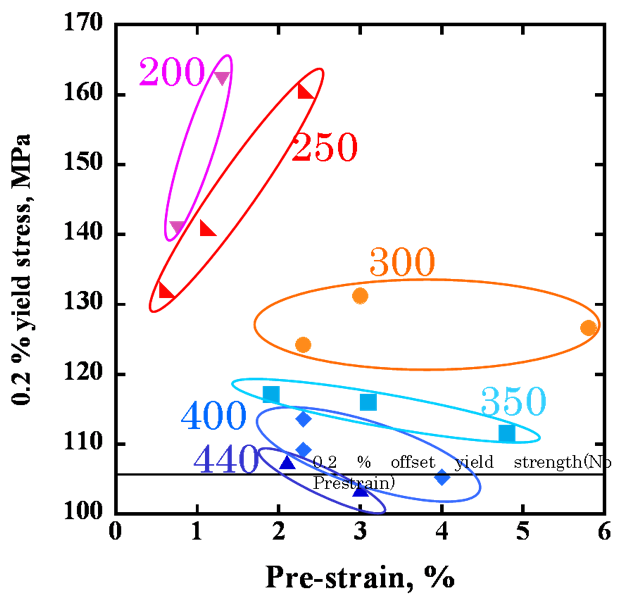
結論
以上の研究成果は、2012 年度第 160 回鋳造工学会全国講演会で発表しました。現在、当グループでは、(1)FCD合金の高温で発生する非弾性ひずみが室温での加工硬化に及ぼす影響を定量化すること、(2)上記JIS AD 12.1合金の高温で発生する非弾性ひずみの室温での加工硬化の影響を熱応力解析に取り込み、鋳造時の残留応力を予測する方法を検討することに取り組んでいます。
イントロダクション
熱応力解析には構成方程式が重要です。構成方程式とは材料の応力とひずみの関係式であり、実際の鋳造時の製品の挙動を数値的にシミュレーションするために用いられます。しかし、鋳造は高温域を含むため、弾性・塑性挙動に加えて粘性挙動が生じることが知られています。そこで、この粘性挙動を構成式でモデル化するために「クリープ特性」が必要となります。従来、クリープ特性の取得は引張試験によって行われてきましたが、任意の温度で何度も試験を行う必要があり、時間とコストがかかります。そこで近年、短時間・低コストでクリープ特性を取得する方法として「応力緩和法」が提案されています。応力緩和法は、任意の温度で1回の試験を行うだけでクリープ特性を取得できる利点がある一方、鋳造合金を対象とした検証研究はこれまで行われていません。当研究室では、ニーズの高い鋳造合金(ADC12)のクリープ特性を取得するため、応力緩和法の検証に取り組んでいます。
実験
図1は応力緩和試験の模式図です。応力緩和試験では、まずひずみ速度を一定に保ち、任意のひずみ量に達するまで引張を加えます。このときの時間をt1とします。その後、t1からある時間t2までひずみ量を一定にします。t1からt2までは、図2に見られるように、記録された応力は減少(緩和)します。この緩和曲線からクリープ特性を求めることができます。上記の方法を検証するために、このような「応力緩和試験」で得られたクリープ特性を、従来の引張試験法で得られたクリープ特性と比較します。図3に油圧サーボ疲労試験機、図4に応力緩和法を実施する試験片を示します。
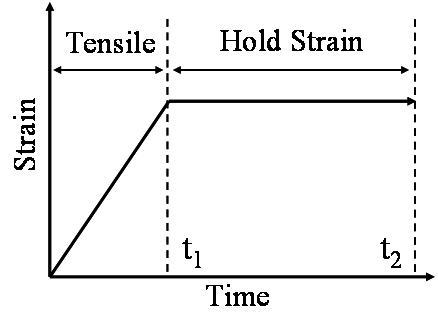
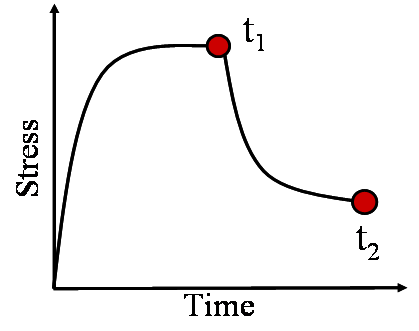
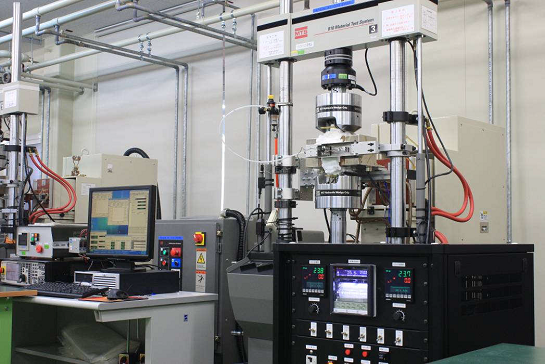
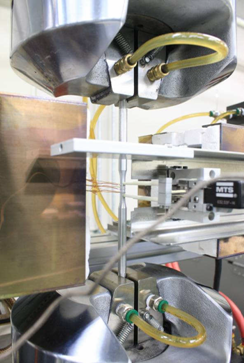
結論
我々は、ADC12のクリープ特性を、従来の引張試験法と新たに提案した「応力緩和法」の両方によって求めてきました。現在、応力緩和法で得られたADC12のクリープ特性の検証を進めています。
イントロダクション
鋳造時には、構成部材の冷却速度の違いにより鋳造製品に残留応力が発生し、一般に残留応力は2つに分けられます。1つ目は、部材の厚肉部と薄肉部の冷却速度差に起因して発生する残留応力。(以下、残留応力(1)、図1参照)2つ目は、部材の同一断面における中央部と表面部の冷却速度差に起因する残留応力(以下、残留応力(2)という。)とします。従って、鋳造製品に発生する残留応力は、残留応力(1)と残留応力(2)の総和となります。しかし、残留応力(2)を解析と比較した研究はありませんでした。すなわち、今回の鋳造品に発生する残留応力の予測精度は不明です。そこで、本研究では、まず鋳鉄の自拘束鋳造形状(応力格子)を用いて鋳造実験を実施しました。そして、残留応力(1)と(2)を測定し、数値解析結果と比較しました。残留応力(1)と(2)の両方を考慮して、鋳造製品に発生する残留応力の解析精度を調べたのは、我々のグループが世界で初めてです。
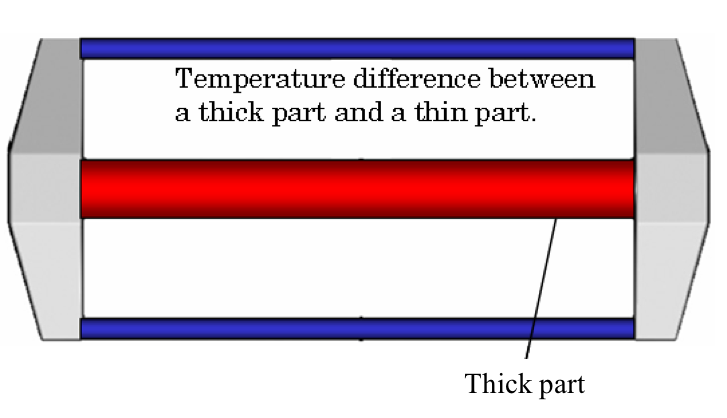
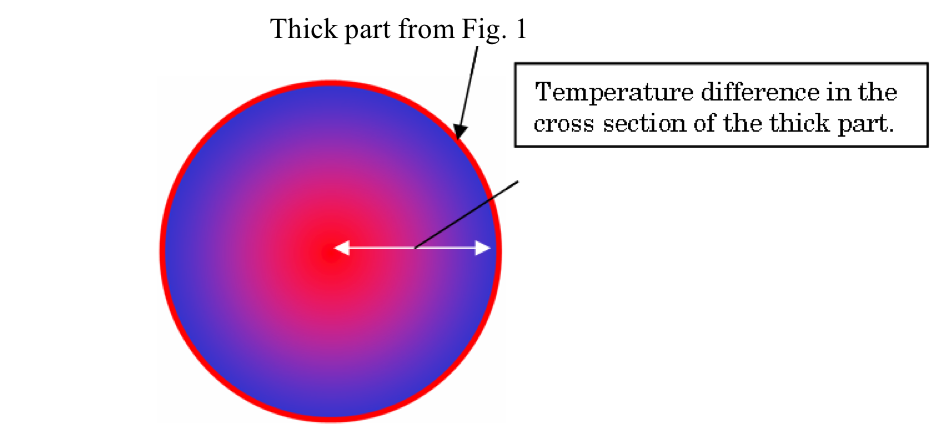
実験
実験に使用した自硬性鋳型の形状と寸法を図3に示す。鋳型は自硬性フラン砂型を用いた。鋳造合金はJIS FC 300を用い、1415℃で注湯した。鋳造温度が150℃以下になった時点で鋳型をノックアウトしました。その後、残留応力(1)および(2)を測定しました。残留応力(1)は、鋳物の厚肉部をハンドソーで切断し、鋳物の長手方向に貼付したひずみゲージで解放ひずみを測定して求めました。一方、残留応力(2)は、円筒状の試験片の軸心を順次円筒状に穿孔した際に、試験片(厚肉部)の外周面に解放されるひずみを測定して求めました。熱・熱応力解析には、前回と同じ弾塑性モデルを用い、FEMソフトウェアAbaqusを用いて数値シミュレーションを実施し、熱応力解析には六面体一次要素を用いました。弾塑性解析は、鋳鉄の構成方程式としてフォンミーゼ降伏条件、等方硬化則、関連フロー則を用いて行いました。数値モデリングに必要な室温から1000℃までの真の応力-塑性ひずみ曲線は引張試験により求めた一方で、熱膨張係数は熱機械分析により弾性率は非破壊法により求めました。
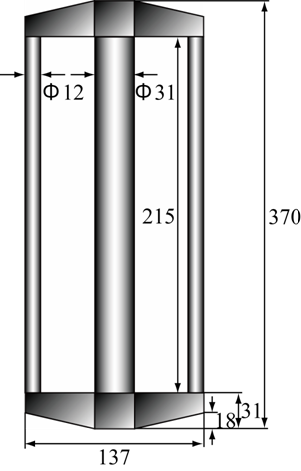
結果
残留応力 (1) の実験値は 56.8 MPa でしたが、解析値は 52.0 MPa であり、シミュレーション誤差は 8.5% 未満であると推測されます。 一方、(2)の残留応力の実験値は1MPa~5MPa程度であるのに対し、解析値は16MPa~19MPa程度であり、実験値と解析値には一桁の差があることがわかりました。 前回研究と同様の弾塑性モデルを用いた結果、鋳物の凝固終了直後に発生する残留応力(2)の発達に伴う厚肉部の熱応力が発生した。 ただし、凝固が完全に終了した後でも、高温域では粘性により熱応力の緩和が起こります。 つまり、先行研究における弾塑性解析において、(2)の残留応力の過大な推定が行われている可能性があると考えられます。 本研究では、これまでの弾塑性モデルに加えて、「機械的融解温度」と呼ばれる温度を導入しました。 この温度を超えると、高温での熱応力の緩和を模倣するために、変形抵抗が無効になります。 図4に残留応力(1)+(2)の実験値、従来の弾塑性モデルを用いた熱応力解析値、機械的溶融温度導入後の熱応力解析を示します。 図4からわかるように、残留応力(2)の解析精度が向上し、それに伴って残留応力(1)+(2)の解析精度も向上しました。
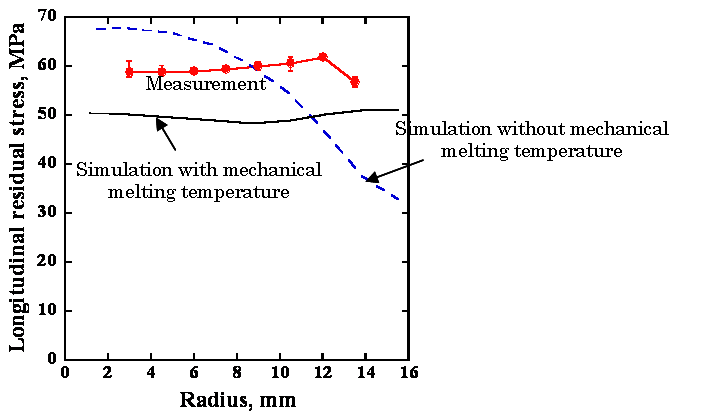
結論
世界に先駆けて自己拘束鋳物の断面における残留応力分布(残留応力②)を実験的に測定し、数値解析と比較しました。 従来の弾塑性モデルでは残留応力(2)の解析値と実験値に大きな差がありました。 上記問題の解決策として、機械的溶融温度を導入して高温での熱応力の緩和を考慮した場合、残留応力(1)+(2)の解析値は実験値に大幅に近づきました。
イントロダクション
近年、環境や安全の問題から、自動車の軽量化の要求に応えるため、エンジンのシリンダブロックの材質変更や薄肉化が盛んに行われています。 シリンダブロックは、JIS ADC12のアルミニウム合金を使用したダイカストで製作されています。ピストンリングの前後運動による磨耗を防ぐため、シリンダブロックの内側には鋳鉄製のシリンダライナが鋳込まれています。現在、シリンダブロックは鋳造時に発生する残留応力によるボアの変形が問題となっています。 本研究では、以上のようにシリンダブロックに発生シリンダブロックの残留応力に起因するボアの変形をCAEで予測することを目的としています。 まず、予測精度を評価するために、ブロックの内側に鋳鉄ライナが溶接されたアルミニウム合金製の単一のシリンダブロックに焦点を当てます。
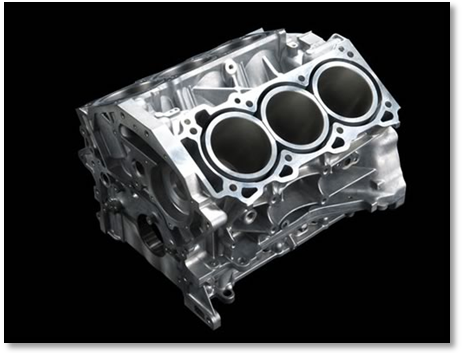
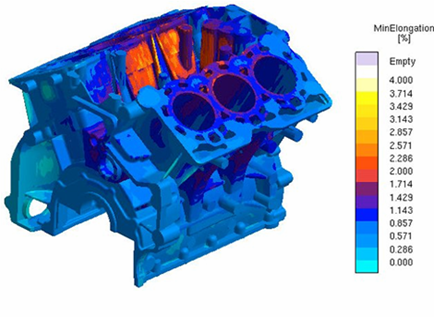
出版
Achim Egner-Walter:20th CAD-FEM User’s Meeting 2002 International Congress on FEM Technology,(2002),1-6
イントロダクション
JIS ADC 12製品は熱処理時に発生する残留応力とそれに伴う変形が問題となる場合がありますが、近年ではCAEを用いた熱応力解析による予測が一般的となっています。私たちのグループはこれまでに、高温で発生したひずみが低温での加工硬化に寄与しないとみなすこと(以下、硬化パラメータのリセット)により、残留応力の弾塑性解析精度が向上することを報告してきました。 現在、人工時効熱処理時に発生する残留応力の予測を目指し、数値シミュレーションの精度向上に取り組んでいます。
実験
図1(a)、(b)に実験に用いた試験片の形状を示します。図1(a)の試験片を470℃の炉に1時間保持した後、水温23℃で水焼入れと人工時効を行いました。フライス盤を使用して直径3mmの貫通穴を開けた後、ワイヤ放電加工機を用いて穴径を3mmずつ大きくし、33mmまで加工しました。解放されたひずみを測定し内部応力がSachs方程式を使用して計算され、残留応力と変形を予測する数値シミュレーションはFEMソフトウェアAbaqusを用いて実施しました。
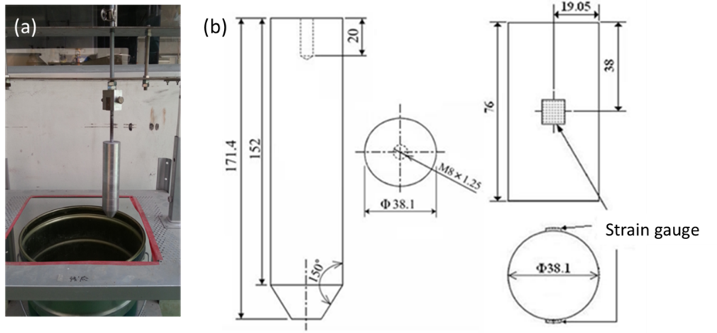
イントロダクション
アルミニウム合金製品の熱処理時に発生する残留応力とそれに伴う変形が問題となる場合がありますが、近年ではCAEを用いた熱応力解析による予測が一般的となっています。 私たちのグループは、JIS ADC12円筒試験片に水焼入れを施して発生する残留応力を弾塑性モデルを用いて予測したところ、高温で発生したひずみは低温での加工硬化に寄与しないことを報告しています。このようにして、高温における合金のひずみ速度依存性が解析精度に及ぼす影響を調査しました。.
実験
Fig. 1 (a) 水焼入れ試験片、(b) 残留応力測定片の寸法。 (c) 本研究で得られた結果
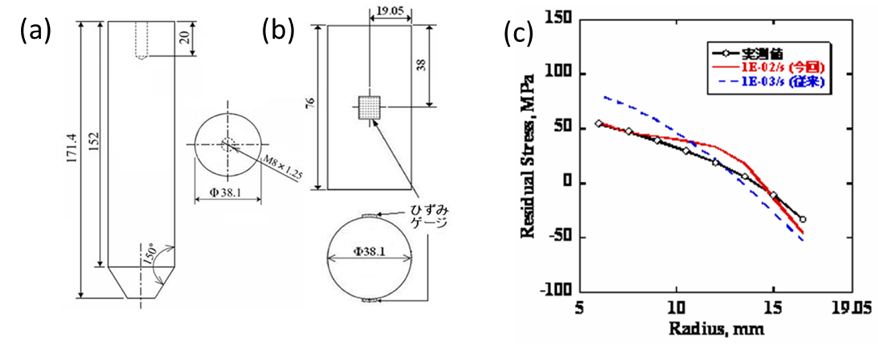
Conclusion
図1(c)は、試験片の長手方向の残留応力分布の実験結果と解析結果を比較したものです。高温で発生したひずみが低温での加工硬化に寄与しないことを考慮することで弾塑性解析精度が,高温における合金の機械的性質のひずみ速度依存性を考慮することにより解析精度が向上することがわかった。したがって,水冷を受けるアルミニウム合金の残留応力を予測する際には,上記2つの項目を考慮する必要があることが示唆された。
私たちの研究で実施したいくつかの鋳造シミュレーションと実験のビデオを以下に示します。
-
大型FC鋳物解析
-
大型FC鋳物解析(変位20倍)
-
鋳鉄応力格子の鋳造
-
切削法による鋳鉄応力格子の残留応力の解放